Continuous Casting Industry
Continuous casting industry In recent years, advanced production methods such as direct continuous (or semi-continuous) production of bars or tubes from molten metal state are being promoted at home and abroad. Artificial graphite is considered a suitable material as a mold for continuous or semi-continuous casting of non-ferrous metals. Production practice has proved that the continuous casting industry uses graphite molds because of its good thermal conductivity (the thermal conductivity determines the solidification speed of the metal or alloy), and the good self-lubricating performance of the mold. High dimensional accuracy, smooth surface, uniform crystal structure, and can be directly processed in the next process. This not only greatly improves the yield and reduces waste loss, but also greatly improves product quality. There are two types of continuous casting methods: vertical continuous casting and horizontal continuous casting.
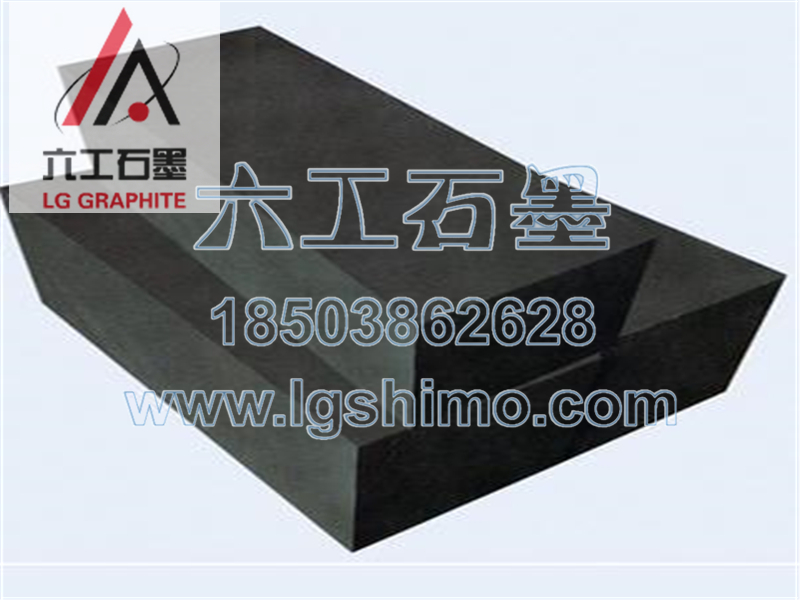
Continuous casting graphite molds are also used in the metal smelting industry, where molten metal can be cast with graphite molds. Graphite molds are reusable, but there are some designs that can only be used once. Creative small grain castings can be cast directly using graphite molds.
The coefficient of thermal expansion is an important factor in determining the use of graphite as a mold material. A casting mold is a medium with a very non-uniform temperature, from being hot from the inside due to the molten material to being cold on the outside due to the cooling process applied to it. The low coefficient of thermal expansion exhibited by graphite allows the mold to function without deforming or cracking. Another very important factor is self-lubrication. Graphite is a solid lubricant that creates low friction between the mold and the casting material. Subsequently, the graphite can smoothly extract the casting.
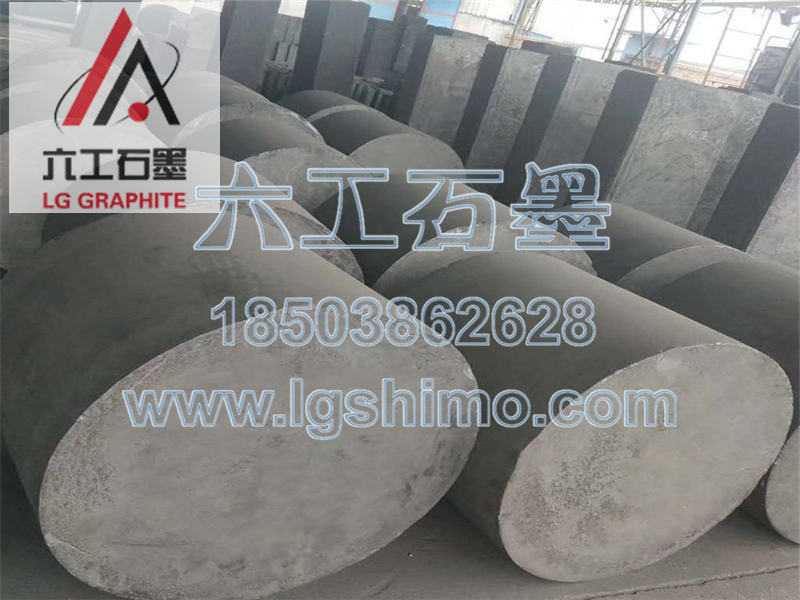
There are many factors that determine the life of continuous casting graphite molds. From the composition of the casting material, to the casting temperature, to the cooling rate, the life of the graphite mold will be affected. The specific graphite grade used is also determined by a variety of factors. The main factor is which material process field the mold to be cast is used for. For example, for grey cast iron or high nickel alloys, high temperature resistant graphite is required, while for brass a relatively dense graphite with sufficient open porosity to allow zinc evaporation would be a good choice.